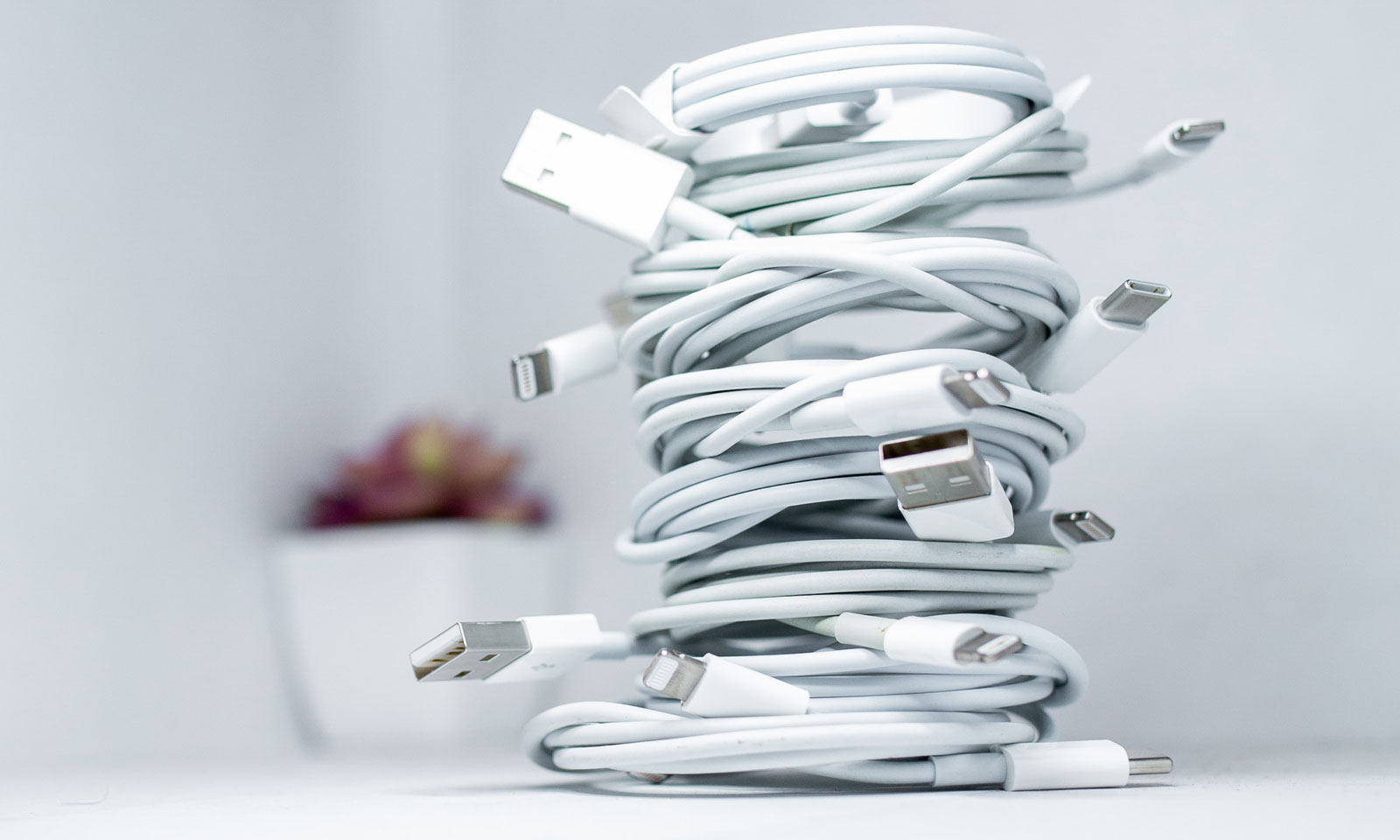
BS 6396 with Phil Reynolds
Monthly Column By Phil Reynolds
I thought this month I’d introduce one of our newest standards:
BS 6396:2022 – ‘Electrical systems in furniture. Specification’
The standard has a long history within the office sector, where it was used to guide the correct installation of electrical power and data systems, primarily in office desks.
Times have changed however, and we want to charge our phone, or use our laptop everywhere, whether it’s a hotel room, train station, airport or motorway services. This has led to a proliferation of electrical power systems being integrating into all types of furniture including chairs, tables, beds, storage, headboards – pretty much anything.
So, when it was decided to update the standard, the committee – ably chaired by the BCFA’s Jeremy Stein – decided to extend the scope of the standard to cover the installation of electrical systems in all types of furniture, and all applications. The only stipulation is that the system is connected to the building’s mains by a 13 Amp plug – or battery powered.
What’s great about the new standard is that if finally gives all types of furniture manufacturers and designers the information they need to incorporate such systems into their furniture, and how to comply with the appropriate legislation, the snappily titled ‘The Low Voltage Electrical Equipment (Safety) Regulations 1989, as modified by the Product Safety & Metrology etc. (amendment etc.) (EU Exit) Regulations 2019’.
As well as installing the correct electrical equipment the standard covers how to test the system, what markings are needed and what instructions are needed – so a comprehensive piece of work.
One word of warning though, the standard doesn’t cover motorised furniture – which are becoming more common, from height adjustable tables and desks, adjustable beds to reclining and moving seats in cinemas. Because these items move, they present additional risks – indeed we have seen fatalities in the UK. These products are considered as machines, and as such will need to have the relatively new UKCA mark, introduced following the UK leaving the EU (indeed the requirements are currently very similar to the European CE mark), and comply with a different piece of legislation, the equally snappily titled ‘The Supply of Machinery (Safety) Regulations 2008, as modified by the Product Safety & Metrology etc. (amendment etc.) (EU Exit) Regulations 2019’.
The big problem is that there are currently no ‘designated standards’ that manufacturers can use to offer a presumption of conformity to the regulations. Whilst I’m working on two standards that are in development in Europe to cover this type of product, I don’t expect that these will be published until 2024. This means that manufacturers will need to carry out their own risk assessment and ensure compliance with the UKCA requirements, and as there a considerable number of ‘Essential Health and Safety Requirements’ that have to be considered, I’d strongly recommend consulting an expert for help with this process.